Cost Analysis of Concrete Buildings and Their Environmental Impact
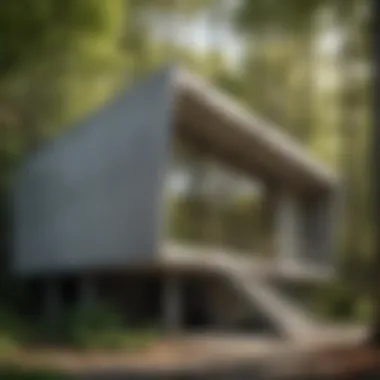
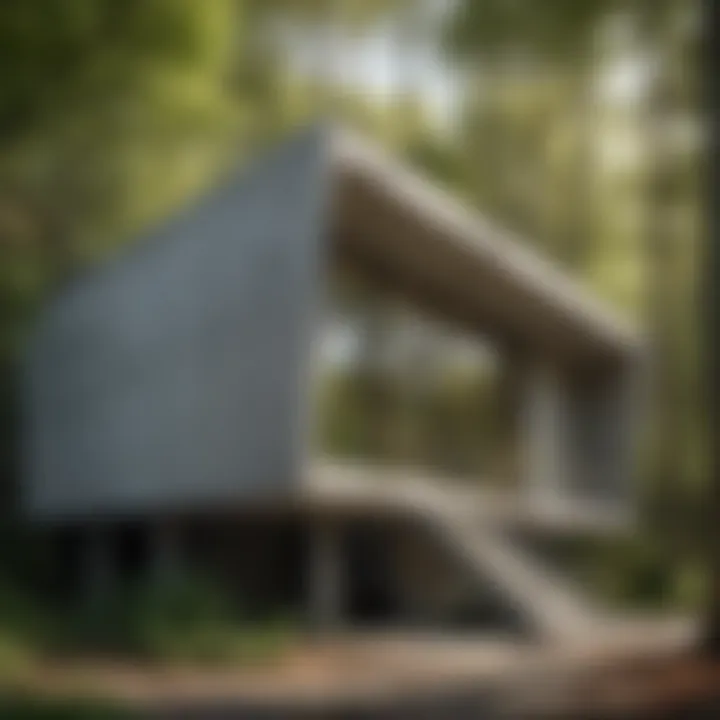
Intro
The consideration of costs in concrete building extends beyond financial metrics. An analysis encompasses various elementsβeconomic, ecological, and socialβthat impact the construction industry. This framework is essential for understanding the multifaceted effects of concrete usage on the environment. Knowledgeable stakeholders, ranging from construction professionals to environmental scientists, can benefit from this comprehensive exploration.
Concrete is a widely recognized building material, yet its implications require scrutiny. This article intends to dissect how construction practices can align with principles of sustainability while maintaining economic viability. It will address forest ecology, sustainable forestry practices, and community engagement. Each section aims to reveal critical insights, making the case for a smarter approach to building.
Forest Ecology and Biodiversity
Importance of Forest Ecosystems
Forests are vital for maintaining ecological balance. They provide essential services, including carbon sequestration, habitat for wildlife, and prevention of soil erosion. With increasing demand for concrete, the pressure on forest resources intensifies. It is crucial to understand how concrete production impacts forest ecosystems.
Flora and Fauna in Woodlands
Forests host diverse flora and fauna, each playing significant roles in their ecosystems. Certain species rely on forest environments for shelter, while others contribute to pollination and seed dispersal. If deforestation occurs to meet concrete demands, the delicate balance of these ecosystems can be disrupted, leading to a loss of biodiversity. This poses challenges for forest conservation.
Sustainable Forestry Practices
Techniques for Responsible Management
Sustainable forestry is key in reducing environmental damage from concrete production. Implementing practices like selective logging, replanting, and habitat preservation helps protect forest ecosystems. These techniques facilitate ongoing resource availability without compromising ecological integrity.
Certification Schemes and Standards
Several certification programs exist to ensure responsible forestry. The Forest Stewardship Council (FSC) and the Programme for the Endorsement of Forest Certification (PEFC) set standards that promote sustainable management. Such certifications encourage consumers to choose responsibly sourced materials, contributing to a balanced approach to concrete use in construction.
Community Engagement and Stewardship
Role of Local Communities
Local communities play a critical role in sustainable forestry practices. Their insights and needs must be taken into account during planning and implementation. Engaging communities fosters stewardship, leading to better management of forest resources. This collaborative approach can help ensure that economic growth does not come at the cost of ecological health.
Volunteer Opportunities for Engagement
Various initiatives invite community members to participate in forestry stewardship. Volunteer programs offer hands-on experience in conservation efforts. Not only do they enrich community ties, but they also educate participants about the importance of sustainable practices. Such engagement can create a ripple effect that fosters a culture of sustainability across regions.
"Only through concerted community efforts can we hope to nurture our forests while meeting the demands of modern construction."
In summarizing these key points, it is evident that analyzing the cost of concrete building involves understanding its impact on forest ecology and seeking sustainable alternatives. The path towards more ecologically responsible construction practices is contingent upon collaboration among professionals, communities, and the forestry sector.
Ultimately, the integration of concrete building into a sustainable framework should strive for a balance that benefits both economic development and environmental conservation.
Preamble to Concrete Building Costs
The topic of concrete building costs encompasses several crucial aspects that directly influence not only construction budgets but also the environmental implications associated with these projects. Understanding the elements that contribute to concrete costs is essential for architects, builders, and environmental scientists alike. By analyzing these factors, stakeholders can make informed decisions that align with both economic and ecological goals.
Recent trends show that the cost of concrete in construction is steadily rising. This increase impacts project feasibility and sustainability considerations. Thus, it is important to address these costs comprehensively. This section will help outline both the direct and indirect influences affecting pricing in the concrete industry, serving as a foundational understanding for deeper insights offered in subsequent sections.
Definition of Concrete in Construction
Concrete is a versatile building material made from a mixture of cement, water, aggregates, and often additives. It gains strength through a chemical process known as hydration. This makes concrete durable, strong, and built to last. Its prevalence in construction stems from its adaptability, enabling its use in everything from residential buildings to large infrastructure projects.
Key aspects of concrete include:
- Durability and Longevity: Concrete structures often last for decades, indicating long-term value.
- Energy Efficiency: Concrete can contribute to energy-efficient buildings due to its thermal mass properties.
- Sustainability Potential: There are ongoing innovations in concrete production that aim to reduce environmental impacts.
These characteristics make concrete a staple in the construction industry. However, its production and use also pose environmental challenges that should not be overlooked.
Market Factors Influencing Cost
Several market-related factors significantly dictate the costs associated with concrete in construction. Grasping these factors helps stakeholders navigate the intricacies of budgeting effectively.
- Raw Material Prices: The cost of key ingredients, such as cement and aggregates, can fluctuate based on supply and demand dynamics. Global events like natural disasters can disrupt supply chains, leading to sudden price surges.
- Labor Expenses: With the construction industry facing labor shortages, wages tend to rise. Skilled labor is essential for both the proper mixing of concrete and the execution of its application on-site.
- Regulatory Policies: Government regulations can also influence costs through permits and environmental assessments. Stricter standards may require more comprehensive studies and additional investments.
Studies show that regulatory compliance can add up to 20% to overall project costs, heavily impacting budget allocations.
- Market Demand: In areas where demand for new constructions is high, costs may rise correspondingly. This may create a ripple effect across related sectors, such as equipment rentals and logistics.
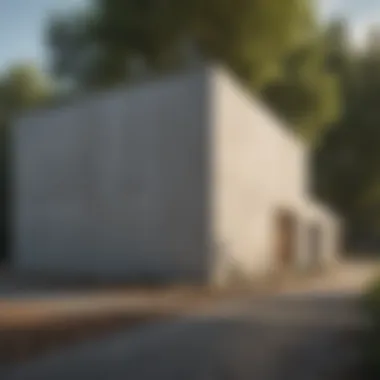
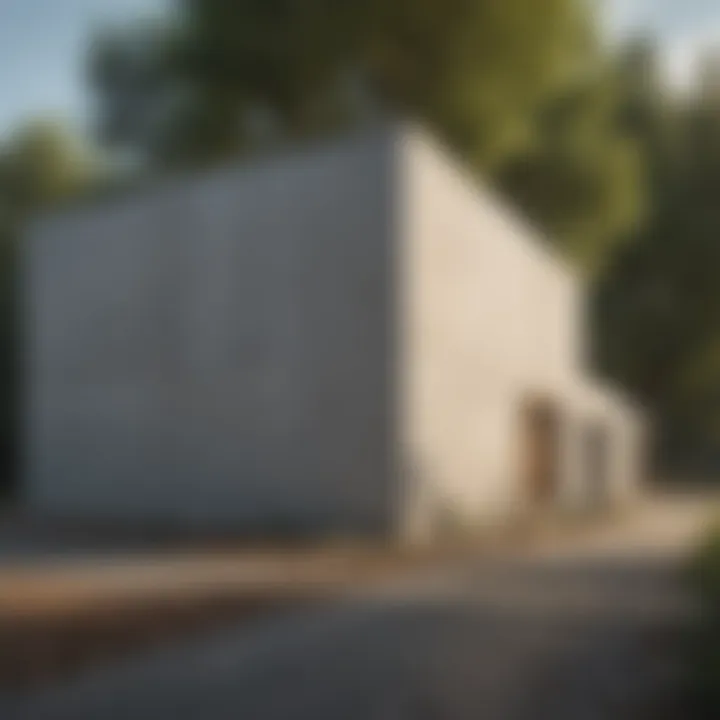
Understanding these market factors is thus integral for professionals involved in construction. This knowledge helps in strategic planning and in adopting best practices for budget management.
Components of Concrete Costs
Understanding the components of concrete costs is essential in analyzing the overall financial impact of concrete construction. This section identifies and explains the various elements that contribute to the total cost of concrete buildings. These components not only influence construction budgets but also have implications for environmental sustainability and resource management.
Material Pricing and Sourcing
Material pricing is a critical component of concrete costs. The price of raw materials, such as cement, aggregates, and admixtures, fluctuates based on market dynamics and local availability. For example, the quality of cement can significantly impact its price. Sourcing materials from local suppliers may reduce transportation costs, but it is vital to assess their sustainability practices as well. Local sourcing can minimize the carbon footprint associated with transportation.
When purchasing materials, companies should consider grade and quality specifications, ensuring compliance with relevant standards. Additionally, the use of recycled materials, such as crushed concrete, can result in cost savings while promoting sustainability. This approach helps reduce waste and utilize existing resources more efficiently.
Labor Costs and Workforce Dynamics
Labor costs represent another significant aspect of concrete building expenses. This includes wages, benefits, and overhead for workers involved in the construction process. Labor rates can vary based on geographic location, project size, and project complexity. Skilled labor may command higher wages, but their expertise can lead to better-quality work and efficiencies in time and material usage.
Workforce dynamics play a crucial role in cost estimation. On-site conditions, such as weather or regulatory requirements, can affect productivity. Furthermore, investing in training and development of the workforce can lead to more efficient practices, ultimately reducing costs in the long term. Companies should also consider labor availability, as regions with skilled labor shortages may see increased wage demands, impacting overall project budgets.
Transportation and Logistics Expenses
Transportation and logistics are key factors influencing the cost of concrete construction. These expenses involve the movement of raw materials to the site and the distribution of finished concrete. Costs can vary based on distance, fuel prices, and the mode of transport used.
Logistical challenges, such as insufficient infrastructure or traffic congestion, can also increase costs and project timelines. Efficient planning and coordination are vital to minimize these expenses. Implementing just-in-time delivery systems can help keep material costs down and reduce on-site waste.
Conclusion: Understanding the components of concrete costs is vital for professionals involved in construction and environmental sustainability. By analyzing material pricing, labor dynamics, and transportation logistics, stakeholders can make informed decisions that align with financial goals while also considering environmental impacts.
Lifecycle Cost Analysis
Lifecycle cost analysis (LCA) is a crucial concept in the context of concrete building. It encompasses the full spectrum of expenses associated with a concrete structure from inception to demolition. Understanding LCA is vital for stakeholders. It facilitates informed decision-making, especially when evaluating long term sustainability and cost implications. By incorporating both direct and indirect costs, LCA provides a comprehensive view that extends beyond initial investment.
LCA typically looks at several vital components. These include initial construction costs, maintenance and operational expenditures, as well as disposal and environmental remediation costs. By analyzing these components, professionals can identify hidden costs that often go overlooked. This understanding can significantly influence material selection and construction methods.
Benefits of Lifecycle Cost Analysis:
- Comprehensive Perspective: LCA provides a holistic view of costs over time.
- Informed Decisions: Helps in choosing materials that align with budget and environmental goals.
- Long-term Planning: Encourages considering future expenses in the decision-making process.
- Sustainability Focus: Supports the identification of practices that minimize ecological impacts.
In summary, lifecycle cost analysis serves as a vital tool for assessing the economic and environmental implications of concrete building. Stakeholders benefit from examining all cost factors, leading to potentially more sustainable and economically viable construction practices.
Initial Investment and Construction Expenses
The initial investment in concrete construction forms the foundation of any lifecycle cost. This encompasses the costs of materials, labor, and equipment utilized during the construction phase. Material pricing often dictates the budget. Factors such as supply chain dynamics, local market conditions, and material quality play substantial roles here. For instance, higher-quality concrete may demand a premium price but offer enhanced durability and lesser maintenance costs over time.
Additionally, labor costs vary significantly based on regional economics and workforce skill levels. Effective project management can help minimize these costs, but unforeseen labor issues can lead to considerable overruns.
Maintenance and Operational Costs
Once construction is complete, ongoing maintenance comes into play. Maintenance costs can include routine inspections, repairs, and upgrades necessary to ensure the structure remains safe and functional over time. Operational costs might also include expenditures related to energy efficiency. Well-designed structures can lower energy usage, making the management of operational costs an essential factor in long-term financial planning.
Regular maintenance on concrete structures is necessary to prevent deterioration. Costs related to sealants, resurfacing, or even major repairs can add up quickly. This can be a significant factor in a structure's total lifecycle cost.
Disposal and Environmental Remediation Costs
As concrete buildings reach the end of their useful lives, disposal becomes necessary. Concrete disposal can involve significant expenses, especially when considering environmental remediation. The primary concern here is ensuring that demolished concrete does not contribute further to ecological degradation. Proper disposal strategies can help mitigate costs, transforming waste into reusable material through recycling initiatives.
Environmental Remediation may involve ensuring compliance with local regulations, which can be costly. Options for remediation will vary widely by region and the severity of contamination caused by concrete production or disposal practices.
Impact of Concrete on the Environment
Concrete is a primary material in construction, but its applications come with significant environmental implications. Understanding the environmental impact of concrete is essential for stakeholders in the construction and forestry sectors. This section focuses on three critical elements of concrete's environmental footprint: carbon emissions, resource depletion, and water usage. Each aspect plays a vital role in guiding the future practices of sustainable construction.
Carbon Footprint and Emission Concerns
The production of concrete is associated with a large carbon footprint. It is estimated that nearly 8% of global carbon dioxide emissions arise from cement manufacturing, a key ingredient in concrete. This process involves the calcination of limestone, which releases a substantial amount of CO2. Moreover, the fossil fuels used to heat the kiln contribute significantly to emissions.
Reducing carbon emissions in concrete production is essential. Utilizing alternative fuels and capturing emissions during production can help mitigate environmental harm. Researchers are focusing on carbon capture technologies that can trap and store emissions before they enter the atmosphere.
"Realizing a reduction in the carbon footprint of concrete begins with awareness and innovation in production methods."
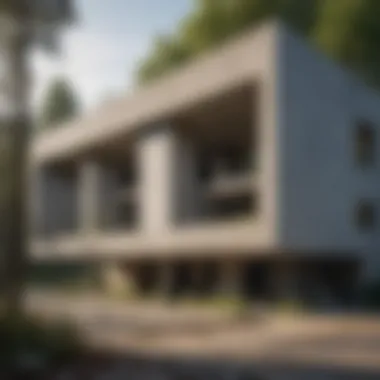
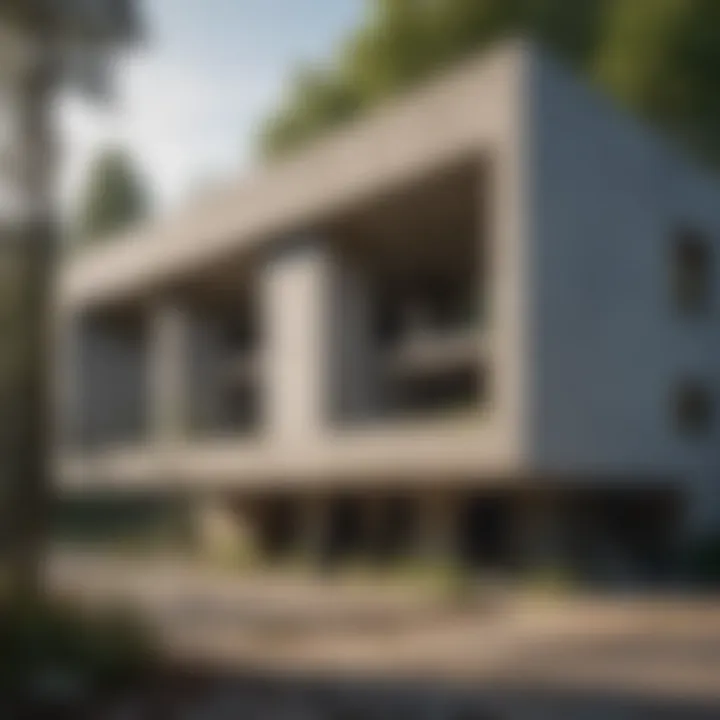
Resource Depletion and Natural Habitat Impact
Concrete production relies heavily on natural resources, including gravel, sand, and water. Extracting these resources can lead to environmental degradation. For instance, sand mining can disrupt local ecosystems and biodiversity. Deforestation and soil erosion are often consequences of increased demand for construction materials.
It is crucial to balance the need for concrete with the preservation of natural habitats. The implementation of sustainable extraction practices can lessen harm. Sustainable quarrying and regulatory frameworks can ensure that resource depletion does not compromise environmental integrity.
Water Usage and Management in Concrete Production
Water is an essential component of concrete. However, its usage raises concerns, particularly in water-scarce regions. The concrete industry can consume large quantities of fresh water, affecting local water supplies and ecosystems.
Management of water resources during concrete production is vital. Techniques such as using recycled water and improving efficiency can help reduce freshwater consumption. Additionally, developing concrete mixtures that require less water can mitigate the environmental impact of production.
In summary, recognizing the environmental consequences of concrete is vital for making informed decisions. Understanding the carbon footprint, resource depletion, and water consumption can guide more sustainable practices in the concrete industry.
Sustainability in Concrete Construction
Sustainability in concrete construction plays a crucial role in addressing the environmental impacts of building practices. As the global focus shifts towards minimizing ecological footprints, integrating sustainable methods into concrete production and use becomes increasingly essential. This section explores key elements, benefits, and considerations surrounding sustainability in concrete construction, shedding light on how current practices can evolve for the better.
Innovative Concrete Technologies
Innovative concrete technologies are at the forefront of sustainable construction practices. These advancements aim to enhance the performance of concrete while reducing its environmental impact. For instance, using lighter aggregates or incorporating industrial by-products like fly ash or slag can improve the sustainability of concrete mixtures.
Benefits of Innovative Technologies:
- Reduced Resource Consumption: Innovative techniques often require fewer natural resources in the mix design. This lowers the demand for conventional materials.
- Improved Durability: By enhancing the lifespan of concrete structures, maintenance and repair needs are minimized. Reduced maintenance translates to lower financial and environmental costs over time.
- Energy Efficiency: Some modern systems employ energy-efficient methods during production, minimizing the carbon footprint associated with mixing and curing concrete.
Emerging technologies such as high-performance concrete and self-healing concrete demonstrate the potential for significant sustainability advancements in the concrete industry.
Recycling and Reusing Concrete Materials
Recycling and reusing concrete materials encapsulates another vital aspect of sustainability. As construction generates a substantial amount of waste, managing this waste effectively is essential to mitigate environmental harm.
Key Approaches to Recycling Concrete:
- Crushed Concrete Aggregate (CCA): One common practice is to crush demolished concrete and use it as aggregate in new concrete. This not only decreases waste but also reduces the need for virgin materials.
- Reclaimed Water Utilization: Employing recycled water in concrete production helps to conserve fresh water, which is increasingly becoming a scarce resource in many regions.
Applying these methods can significantly lower the environmental impacts associated with concrete production. Industry stakeholders can also gain economic advantages by opting for recycled materials, contributing to a circular economy in construction.
Certifications and Standards for Sustainable Practices
The establishment of certifications and standards for sustainable practices in concrete construction helps ensure that performance metrics are met while promoting environmentally-friendly methods. Recognized certifications provide a framework for measuring sustainability in material sourcing, production, and overall lifecycle impacts.
Prominent Certifications Include:
- Leadership in Energy and Environmental Design (LEED): This certification addresses a building's sustainability concerning energy efficiency, water usage, and materials. Concrete projects can earn points towards LEED certification by integrating sustainable practices.
- Environmental Product Declarations (EPDs): These documents provide transparent information about the environmental impact of concrete products, serving as crucial tools for professionals seeking to make informed decisions based on lifecycle assessments.
Adhering to these certifications encourages the concrete industry to adopt more sustainable practices, garnering trust among clients and stakeholders.
Sustainability in concrete construction is not just an option; it is an imperative for the future of the built environment. By embracing innovative technologies, recycling practices, and rigorous standards, the industry can significantly mitigate its ecological impact.
Alternatives to Traditional Concrete
The exploration of alternatives to traditional concrete is not merely an academic exercise but a necessity in the face of pressing environmental challenges. The construction industry is at a crossroads, where the impact of concrete on the environment prompts a reevaluation of materials used in building. As urbanization continues to rise, so does the scrutiny over the ecological footprint of concrete production and use. Finding viable alternatives can contribute to reduced carbon emissions, less resource depletion, and a generally more sustainable construction practice.
Adopting alternative materials not only allows for innovative building solutions but also cultivates resilience within the construction sector. By integrating options that may be less taxing on the environment, professionals can align their practices with global sustainability goals. Key elements to consider when evaluating alternatives include the raw material sourcing, cost-effectiveness, durability, and overall impact on the lifecycle of buildings.
Comparing Alternative Building Materials
Several materials have emerged as potential substitutes for traditional concrete. Each alternative presents unique characteristics and applications. Some noteworthy materials include:
- Bamboo: Known for its remarkable strength-to-weight ratio, bamboo offers an organic substitute with less environmental impact. It grows rapidly, enabling sustainable harvesting practices.
- Rammed Earth: An age-old technique, rammed earth uses natural soil to form dense building walls, providing thermal efficiency and low-cost production.
- Recycled Aggregates: Using crushed concrete and other materials for aggregate can significantly reduce waste and the need for new raw materials. This practice encourages recycling in construction.
- Geopolymer Concrete: This innovative material is produced using industrial waste and exhibits lower emissions during its production phase. It can achieve similar or even superior strength compared to traditional concrete.
By examining the properties and potential of these materials, stakeholders can begin to understand how they might meet specific construction requirements without compromising environmental integrity.
Pros and Cons of Alternative Materials
Using alternative materials in construction carries both advantages and disadvantages. Understanding these can guide informed decision-making:
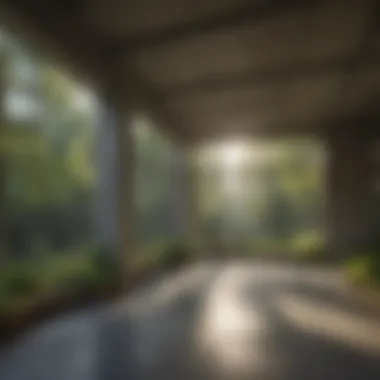
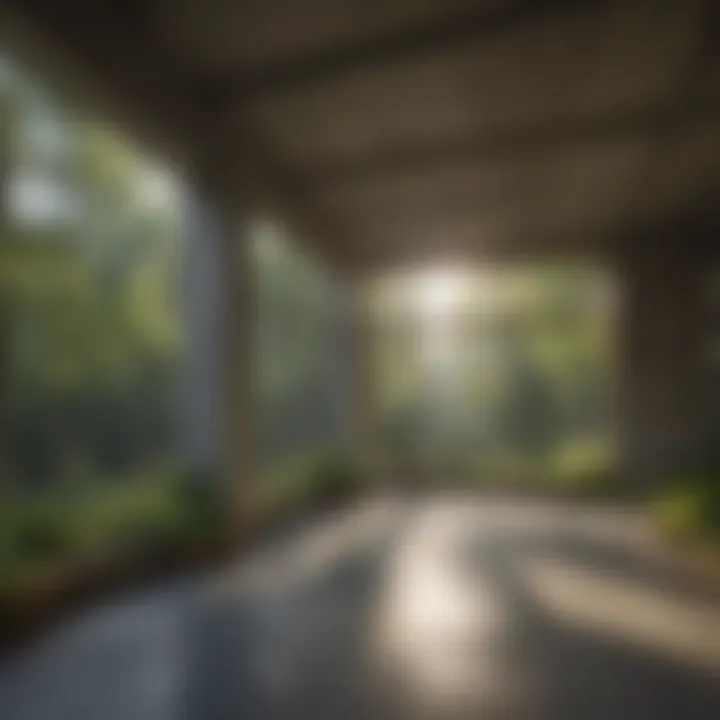
Pros
- Environmental Benefits: Many of these alternatives reduce the carbon footprint associated with concrete. For instance, bamboo captures carbon during its growth.
- Resource Efficiency: Utilizing materials like recycled aggregates diminishes the reliance on quarrying new resources, thus preserving natural habitats.
- Cost-Effectiveness: Over time, some alternatives can yield savings on materials and energy, especially when their inherent properties lend themselves to energy efficiency.
Cons
- Structural Limitations: Not all alternatives may provide the same structural properties as traditional concrete. For example, bamboo may require more attention to joining techniques to ensure stability.
- Economic Viability: Initial costs for some alternative materials might be higher and require a paradigm shift in procurement and construction practices.
- Market Acceptance: There can be resistance from conventional builders to embrace alternative materials due to perceived risks and lack of familiarity, impacting adoption rates.
The shift towards alternatives in building materials is essential for fostering a more sustainable future, linking ecological responsibility with economic viability.
Future Trends in Concrete Building Costs
The concept of future trends in concrete building costs holds significant relevance as it shapes the trajectory of construction within both an economic and environmental context. Understanding where the industry is headed allows stakeholders, from investors to policymakers, to make informed decisions in a climate where sustainability and cost-effectiveness are paramount. As concrete remains a dominant building material, recognizing its evolving dynamics will ensure that the construction sector adapts to shifting market demands and regulatory landscapes.
Emerging Technologies Impacting Costs
Emerging technologies are poised to revolutionize the concrete industry, impacting costs in multiple ways. Innovations such as 3D printing and advanced mixing techniques are streamlining production processes, which can lead to substantial cost reductions. For example, 3D printing in construction not only lowers labor costs but also minimizes waste, leading to a more efficient use of resources. Techniques like self-healing concrete and environmentally-friendly admixtures can enhance the longevity and performance of structures, resulting in lower lifecycle costs.
Moreover, digital tools such as Building Information Modeling (BIM) are now widely used. These tools improve project management and precision in estimating costs from the early stages. By allowing real-time adjustments and foresight into potential issues, BIM can make projects more predictable in terms of budget and timeline.
"Technological advancements in concrete production and management can lead to reduced labor and material costs, making construction more sustainable and affordable."
Regulatory Changes and Market Shifts
Regulatory changes significantly influence concrete building costs. Governments increasingly prioritize environmental sustainability, leading to stricter regulations regarding emissions and resource usage in concrete production. These changes compel manufacturers to invest in cleaner technologies and raw materials, which may initially raise costs.
However, in the long term, such regulations can balance out due to the competitive advantages gained through these practices. Companies adhering to higher sustainability standards may find themselves in a favorable position, capturing a market that increasingly values environmental responsibility. The rise in demand for green building certifications, for example, has influenced both material choices and construction methods.
Market shifts also play a critical role. With rising awareness around climate change and its impact on construction, there is a notable shift towards alternative materials and construction practices. These trends challenge traditional concrete-centric approaches and encourage innovations that may redefine cost structures. As alternatives become more mainstream, old standards may shift, and the expectation for cost-effectiveness coupled with sustainability will become the norm.
Case Studies in Concrete Building
Case studies play a crucial role in understanding both the challenges and successes associated with concrete building practices. They provide real-world examples that illustrate how theoretical concepts manifest in practical applications. By analyzing various projects, stakeholders can gather insights that are directly applicable to their own endeavors. Additionally, case studies highlight innovative sustainable practices and the lessons learned from past experiences, thereby offering an invaluable resource for professionals in construction and environmental sciences.
Successful Implementations of Sustainable Practices
In recent years, numerous projects have showcased successful implementations of sustainable practices in concrete construction. For instance, the Bullitt Center in Seattle, often referred to as the greenest commercial building in the world, integrates concrete with energy-efficient systems. This building employs locally sourced materials, reducing transportation emissions.
Another example is the construction of the Museum of Tomorrow in Rio de Janeiro, Brazil. The design emphasizes the use of sustainable materials alongside concrete, such as recycled aggregates and energy-efficient technologies. These strategies lowered the buildingβs carbon footprint and won multiple awards for innovation in sustainability.
The impact of successful implementations is manifold:
- Reduction in Lifecycle Costs: Sustainable concrete practices often lead to reduced energy bills and maintenance costs over time.
- Enhanced Durability: Using high-performance concrete can increase the longevity of structures, thereby reducing the need for frequent repairs.
- Improved Community Perception: Projects that prioritize sustainability often foster positive perceptions within their community, leading to increased support and partnership opportunities.
Lessons Learned from Cost Overruns
Despite the successes, many projects have encountered significant cost overruns primarily due to insufficient planning or unpredicted material costs. For example, the construction of the London Olympic Park faced numerous challenges related to budget management, leading to discussions about better integrating cost management with sustainability goals.
Key lessons drawn from these cases include:
- Comprehensive Planning Is Essential: All stakeholders must engage in thorough planning phases to anticipate potential challenges.
- Flexibility in Material Sourcing: Adapting to market changes and having alternative suppliers can mitigate unexpected cost spikes.
- Monitoring and Adjusting: Continuous monitoring of budget vs. actual costs is critical. Adjusting strategies as necessary can prevent overruns.
"Cost overruns remind us that sustainability cannot be achieved without careful financial consideration and management."
These case studies provide essential insights for improving future concrete building projects, aligning environmental concerns with budgetary constraints to create more sustainable and economically viable infrastructures.
Closure and Recommendations
The conclusion draws critical insights from the discussions in this article. It does not only emphasize the importance of understanding the cost of concrete buildings but also highlights the various environmental factors connected to concrete production and disposal. Recognizing these costs aids stakeholders in making informed decisions. Such decisions could improve financial performance while adhering to sustainable practices.
Summary of Key Findings
- Economic Aspects: The cost structure of concrete construction is influenced by various market factors. These include material prices, labor costs, and logistics.
- Environmental Impact: Concrete has a significant carbon footprint. The production process contributes to greenhouse gas emissions, highlighting the need for eco-friendly alternatives.
- Lifecycle Consideration: Evaluating the total lifecycle costs, not only initial expenses but also maintenance and disposal, reveals the long-term financial implications of concrete use in building.
- Sustainability Practices: Innovative technologies and recycling methods can mitigate some negative environmental impacts. More emphasis on certifications can assure eco-friendliness in projects.
- Alternatives: Several materials serve as possible substitutes for traditional concrete. Evaluating their viability in specific contexts can benefit environmental goals.
Strategic Recommendations for Stakeholders
- Adopt Lifecycle Assessment: Stakeholders should perform lifecycle assessments for building projects. This approach helps identify long-term costs and environmental impacts systematically.
- Invest in Sustainable Technologies: Support investment in innovative concrete and construction technologies. These technologies can lead to cost savings and reduced environmental harm.
- Encourage Recycling Initiatives: Promote policies that encourage the recycling of concrete. Reusing materials can conserve resources and lower disposal costs.
- Prioritize Education and Training: Educate construction professionals about sustainable practices. Providing training helps integrate eco-friendly strategies into daily operations.
For any progress in reducing the concrete industry's impact, collaboration across various sectors is essential. A unified approach can lead to significant advancements in both ecological preservation and cost-effectiveness.
- Monitor Regulatory Changes: Stay informed about changes in environmental regulations. Compliance can prevent costly liabilities and support sustainable business practices.
Stakeholders' proactive engagement in these strategies will not just support sustainability but could also lead to financial benefits. The cost of concrete buildings should not be viewed only in monetary terms but as part of a broader environmental responsibility.